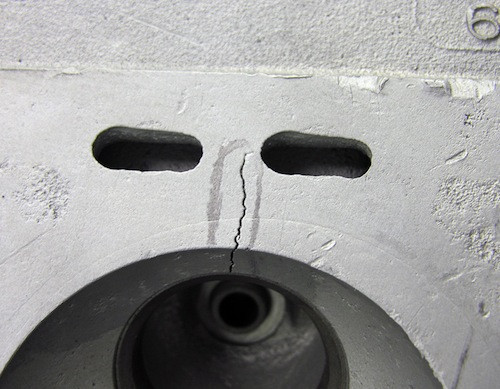
Fixing a cracked head on a car involves several methods, from pinning to welding. CARDIAGTECH.NET offers the tools and expertise needed for each approach. Addressing this issue promptly can prevent further engine damage and costly repairs.
Contents
- 1. Understanding Cracked Cylinder Heads
- 1.1. Identifying the Culprits: Common Causes of Cylinder Head Cracks
- 1.2. Materials Matter: Why Aluminum and Cast Iron React Differently
- 2. Recognizing the Signs: Symptoms of a Cracked Cylinder Head
- 3. Diagnostic Techniques: Finding the Crack
- 3.1. Visual Inspection: A Careful First Look
- 3.2. Pressure Testing: Pinpointing Leaks
- 3.3. Dye Penetrant Test: Revealing Hidden Flaws
- 3.4. Compression Test: Assessing Cylinder Health
- 3.5. Leak-Down Test: Precisely Locating Leakage
- 4. Repair Options: Choosing the Right Method
- 4.1. Pinning: A Stitch in Time
- 4.1.1. Tapered vs. Straight Pins: Making the Right Choice
- 4.2. Welding: Fusing the Fracture
- 4.2.1. TIG Welding for Aluminum: Precision and Strength
- 4.2.2. Furnace Welding for Cast Iron: A Black Art
- 4.2.3. Flame Spray Welding: A Modern Alternative
- 4.3. When Replacement is the Only Option: Knowing When to Quit
- 5. Step-by-Step Guide: Repairing a Cracked Cylinder Head
- 5.1. Preparing for the Task: Essential Tools and Materials
- 5.2. Pinning Procedure: Step-by-Step Instructions
- 5.3. Welding Procedure: Step-by-Step Instructions
- 6. Post-Repair: Ensuring a Lasting Fix
- 6.1. Checking for Warpage: Surface Straightness is Key
- 6.2. Resurfacing: Achieving a Perfect Seal
- 6.3. Valve Job: Optimizing Performance
- 6.4. Reassembly: Precision is Paramount
- 6.5. Coolant System Care: Preventing Future Cracks
- 7. Prevention: Avoiding Cracked Heads
- 8. Cost Considerations: Repair vs. Replacement
- 8.1. Estimating Repair Costs: What to Expect
- 8.2. Assessing Replacement Costs: New vs. Used
- 8.3. Labor Costs: A Significant Factor
- 8.4. Long-Term Value: Weighing the Options
- 9. Professional Help: When to Call an Expert
- 9.1. Complexity of the Repair: Knowing Your Limits
- 9.2. Lack of Experience: Avoiding Costly Mistakes
- 9.3. Specialized Equipment: Access to the Right Tools
- 9.4. Time Constraints: Balancing Time and Expertise
- 10. CARDIAGTECH.NET: Your Partner in Automotive Solutions
- 10.1. Diagnostic Tools: Precision and Accuracy
- 10.2. Repair Equipment: Quality and Reliability
- 10.3. Expert Advice: Guidance and Support
- 10.4. Contact Us Today: Get the Help You Need
- 1. How much does it cost to fix a cracked cylinder head?
- 2. Can a cracked cylinder head be repaired instead of replaced?
- 3. What are the symptoms of a cracked cylinder head?
- 4. What causes cylinder heads to crack?
- 5. Is it safe to drive with a cracked cylinder head?
- 6. How do I know if my cylinder head is warped?
- 7. What is the difference between TIG welding and furnace welding?
- 8. Can I repair a cracked cylinder head myself?
- 9. How important is it to maintain the coolant system to prevent cylinder head cracks?
- 10. Where can I find quality tools and equipment for repairing cylinder heads?
1. Understanding Cracked Cylinder Heads
What is a cracked cylinder head, and why does it matter? A cracked cylinder head refers to fractures in the metal component that seals the top of the engine cylinder. These cracks can lead to significant engine problems, including coolant leaks, oil contamination, and loss of compression. According to a study by the University of Michigan’s Automotive Engineering Department, thermal stress is a primary cause of cylinder head cracks. Addressing a cracked head promptly is crucial to prevent further engine damage and ensure optimal vehicle performance. CARDIAGTECH.NET provides the diagnostic tools and repair equipment necessary to tackle this issue effectively.
1.1. Identifying the Culprits: Common Causes of Cylinder Head Cracks
What factors contribute to the formation of cracks in cylinder heads? Several factors can cause cylinder head cracks.
-
Overheating: A significant cause is engine overheating, which exceeds the metal’s design limits, leading to deformation and cracking.
-
Thermal Stress: Rapid temperature changes can cause stress on the cylinder head, leading to cracks.
-
Loss of Coolant: Insufficient coolant can cause the engine to overheat, increasing the risk of cracking.
-
Detonation: Abnormal combustion can create excessive pressure and heat, which can damage the cylinder head.
-
Improper Installation: Incorrect torque on head bolts or dirty bolt threads can cause uneven stress, leading to cracks.
-
Design Flaws: Lightweight construction or design flaws can make cylinder heads more susceptible to cracking under normal operating conditions.
-
Corrosion: Over time, corrosion can weaken the metal, making it more prone to cracking.
Understanding these causes can help prevent cylinder head cracks and maintain optimal engine health. Regular maintenance and monitoring of engine temperature are crucial preventive measures. CARDIAGTECH.NET offers tools to help you monitor your engine’s health.
Cylinder head showing signs of cracking due to thermal stress
1.2. Materials Matter: Why Aluminum and Cast Iron React Differently
How do the properties of aluminum and cast iron influence cylinder head cracking? Aluminum expands almost twice as much as cast iron when heated, creating a mismatch in expansion rates in bimetal engines with aluminum heads and cast iron blocks. This difference can lead to increased stress and a higher likelihood of cracking in aluminum heads. While aluminum heads are lighter and offer better heat dissipation, they are more susceptible to warping and cracking under extreme temperatures. Cast iron heads, although heavier, are more durable and resistant to cracking but can still suffer damage from severe overheating or detonation.
According to a study by the Society of Automotive Engineers (SAE), the thermal expansion coefficient of aluminum is approximately 23.1 x 10^-6 /°C, whereas cast iron is around 12 x 10^-6 /°C. This significant difference highlights why aluminum heads are more prone to thermal stress-related cracking. Choosing the right tools for the job is essential when working with these different materials; CARDIAGTECH.NET has options for both.
2. Recognizing the Signs: Symptoms of a Cracked Cylinder Head
What are the telltale signs that indicate a cracked cylinder head? Recognizing the symptoms of a cracked cylinder head early can prevent further engine damage. Here are some common indicators:
- Overheating Engine: A cracked head can cause coolant leaks, leading to engine overheating.
- White Smoke from Exhaust: Coolant entering the combustion chamber can produce white smoke from the exhaust pipe.
- Coolant Loss: A noticeable decrease in coolant level without any visible external leaks.
- Milky Oil: Coolant mixing with oil can create a milky or frothy appearance on the dipstick.
- Poor Engine Performance: Loss of compression can result in reduced power, misfires, and rough idling.
- External Leaks: Visible coolant leaks around the cylinder head or engine block.
- Bubbling in Radiator: Air or combustion gases leaking into the cooling system can cause bubbles in the radiator or coolant overflow tank.
- Sweet Smell: A sweet, antifreeze-like smell, particularly noticeable when the engine is running.
- Increased Oil Consumption: Oil may leak into the combustion chamber and burn, leading to higher oil consumption.
- Pressurized Cooling System: Excessive pressure buildup in the cooling system due to combustion gases leaking into the coolant.
If you notice any of these symptoms, it’s crucial to inspect the cylinder head and address the issue promptly. CARDIAGTECH.NET offers diagnostic tools to help identify these problems accurately.
3. Diagnostic Techniques: Finding the Crack
How can you accurately diagnose a cracked cylinder head? Several diagnostic techniques can help pinpoint a cracked cylinder head.
3.1. Visual Inspection: A Careful First Look
What should you look for during a visual inspection of the cylinder head? A visual inspection is the first step in diagnosing a cracked cylinder head. Carefully examine the cylinder head for visible cracks, especially around the combustion chambers, valve seats, and coolant passages. Look for signs of coolant leaks, corrosion, or discoloration. Use a magnifying glass to identify hairline cracks that may not be visible to the naked eye. Also, check for warping or distortion of the cylinder head surface. A thorough visual inspection can often reveal the presence and extent of the damage.
3.2. Pressure Testing: Pinpointing Leaks
How does pressure testing help detect cracks in the cylinder head? Pressure testing involves sealing the cylinder head and applying air pressure to the coolant passages to check for leaks. The cylinder head is submerged in water, and any escaping air bubbles indicate the location of cracks. Pressure testing is an effective method for identifying cracks that may not be visible during a visual inspection. This test is particularly useful for detecting leaks in coolant passages and around valve seats.
3.3. Dye Penetrant Test: Revealing Hidden Flaws
What does a dye penetrant test reveal about cylinder head cracks? A dye penetrant test involves applying a special dye to the surface of the cylinder head, which seeps into any cracks or imperfections. After the excess dye is removed, a developer is applied, revealing the location and extent of the cracks. This method is highly effective for detecting surface cracks and is commonly used on both cast iron and aluminum cylinder heads.
3.4. Compression Test: Assessing Cylinder Health
How does a compression test indicate a cracked cylinder head? A compression test measures the pressure within each cylinder to assess the overall health of the engine. Low compression in one or more cylinders can indicate a cracked cylinder head, as the crack may be causing a loss of pressure. This test helps determine if the cylinder head is sealing properly and can identify issues such as valve problems, worn piston rings, or cylinder head cracks.
3.5. Leak-Down Test: Precisely Locating Leakage
What specific leaks can a leak-down test identify in a cylinder head? A leak-down test involves pressurizing each cylinder with compressed air and measuring the rate at which the pressure leaks out. By listening for escaping air at various points (e.g., exhaust pipe, intake manifold, radiator), the source of the leak can be identified. Air leaking from the radiator indicates a crack in the cylinder head allowing air to enter the cooling system. This test is more precise than a compression test and can help pinpoint the exact location of the leak.
4. Repair Options: Choosing the Right Method
What are the available options for repairing a cracked cylinder head, and how do you choose the best one? Several methods exist for repairing cracked cylinder heads, each with its own advantages and disadvantages. The choice depends on the size, location, and severity of the crack, as well as the material of the cylinder head (cast iron or aluminum).
4.1. Pinning: A Stitch in Time
When is pinning an appropriate method for repairing cylinder head cracks? Pinning is a common technique for repairing small cracks in cast iron and aluminum cylinder heads. This method involves drilling holes along the length of the crack and inserting overlapping pins to fill the crack and prevent it from spreading. The pins are then peened over with an air hammer to seal and blend the surface. Pinning is a relatively simple and cost-effective repair method that doesn’t require special tools or heat. It is best suited for small, non-critical cracks in areas that are not subject to high stress.
4.1.1. Tapered vs. Straight Pins: Making the Right Choice
What are the differences between tapered and straight pins for cylinder head repair, and when should each be used? Tapered pins and straight pins are both used in the pinning method for repairing cylinder head cracks, but they have different characteristics and applications.
-
Tapered Pins: Tapered pins have threads that create an interference fit with the hole, providing a tight seal along the entire length of the pin as it is tightened. These pins pull themselves into the crack, offering superior sealing and support. Tapered pins require careful hand-tapping with a tapered tap.
-
Straight Pins: Straight pins can be installed with an ordinary straight tap and a power drill. They rely on a tapered shoulder or sealer to create a seal. Straight pins are easier to install but may not provide as tight a seal as tapered pins.
The choice between tapered and straight pins depends on the specific application. Tapered pins are ideal for cracks that require a high level of sealing and support, while straight pins are suitable for less critical repairs where ease of installation is a priority.
4.2. Welding: Fusing the Fracture
When is welding the preferred method for repairing cracks in cylinder heads? Welding is a common method for repairing larger cracks in both aluminum and cast iron cylinder heads. The specific welding technique varies depending on the material of the cylinder head.
4.2.1. TIG Welding for Aluminum: Precision and Strength
Why is TIG welding the preferred method for repairing aluminum cylinder heads? TIG (Tungsten Inert Gas) welding is commonly used for repairing cracks in aluminum cylinder heads. This process involves cleaning the cylinder head, grinding out the crack, and preheating the head to eliminate thermal stress. TIG welding uses an alternating current and an inert gas (usually argon) to prevent the formation of aluminum oxide, which can contaminate the weld. The welder melts the surrounding metal and fills the crack with molten metal and filler rod. TIG welding provides a strong, high-quality repair that can restore the cylinder head to its original condition.
4.2.2. Furnace Welding for Cast Iron: A Black Art
What makes furnace welding a specialized technique for repairing cast iron cylinder heads? Furnace welding is a specialized technique for repairing large cracks in cast iron cylinder heads. The cylinder head is preheated to a high temperature (around 1,300 degrees F or 704 degrees C) in an oven to minimize thermal shock and relax the metal. The crack is then welded using a torch, and the head is slow-cooled to prevent cracking. Furnace welding requires significant skill and experience and is often considered a “black art.” It is typically used for high-value castings where the cost of replacement is high.
4.2.3. Flame Spray Welding: A Modern Alternative
How does flame spray welding offer a more efficient approach to repairing cast iron cylinder heads? Flame spray welding is an alternative method for repairing cracks in cast iron cylinder heads. This process involves using a special torch to spray nickel powder onto the crack, which melts and fuses to the sides of the crack. Flame spray welding requires preheating the cylinder head to a lower temperature than furnace welding (around 1,000 to 1,400 degrees F or 538 to 760 degrees C) and results in a strong, long-lasting repair. It is easier to learn than furnace welding and can be completed more quickly.
4.3. When Replacement is the Only Option: Knowing When to Quit
In what situations is replacing the cylinder head the most sensible solution? Despite the various repair methods available, there are situations where replacing the cylinder head is the most practical and cost-effective solution. If the cylinder head has extensive damage, multiple cracks, or is severely warped, the cost of repair may exceed the cost of replacement. Additionally, if the cylinder head is critical to the engine’s performance and reliability, replacing it with a new or remanufactured unit may be the best option to ensure optimal engine health.
5. Step-by-Step Guide: Repairing a Cracked Cylinder Head
Can you provide a detailed guide on how to repair a cracked cylinder head? Here’s a step-by-step guide to repairing a cracked cylinder head, covering both pinning and welding methods:
5.1. Preparing for the Task: Essential Tools and Materials
What tools and materials are essential for repairing a cracked cylinder head? Before starting any repair, gather the necessary tools and materials. This includes:
- Safety Gear: Safety glasses, gloves, and a respirator to protect yourself from debris and fumes.
- Cleaning Supplies: Cleaning solvents, brushes, and rags to clean the cylinder head.
- Diagnostic Tools: Magnifying glass, dye penetrant kit, pressure tester, compression tester, and leak-down tester.
- Pinning Tools: Drill, drill bits, guide fixture, tap, tapered or straight pins, and an air hammer.
- Welding Tools: TIG welder (for aluminum), welding torch, filler rod, preheating oven, and slow-cooling equipment.
- Grinding Tools: Grinder with various bits to remove material.
- Measuring Tools: Straight edge and feeler gauges to check for warpage.
- Reference Material: Vehicle-specific repair manual for torque specifications and other critical data.
5.2. Pinning Procedure: Step-by-Step Instructions
How do you properly pin a cracked cylinder head to prevent further damage? Follow these steps to repair a cracked cylinder head using the pinning method:
- Clean the Cylinder Head: Thoroughly clean the cylinder head with cleaning solvents and brushes to remove any dirt, grease, or debris.
- Identify the Crack: Locate the crack and use a magnifying glass to assess its size and extent.
- Drill Holes: Drill small holes at both ends of the crack to prevent it from spreading. Then, drill holes along the length of the crack at regular intervals, ensuring that the holes overlap slightly.
- Tap the Holes: Use a tap to create threads in the drilled holes.
- Install the Pins: Insert the tapered or straight pins into the holes, tightening them as needed. If using straight pins, apply sealer to ensure a tight seal.
- Peen the Pins: Use an air hammer to peen the pins, deforming them to fill the crack and blend the surface.
- Smooth the Surface: Grind and smooth the surface to remove any excess material and create a flush finish.
- Pressure Test: Conduct a pressure test to ensure that the repair is effective and there are no leaks.
5.3. Welding Procedure: Step-by-Step Instructions
What are the key steps in welding a cracked cylinder head for a durable repair? Follow these steps to repair a cracked cylinder head using the welding method:
- Clean the Cylinder Head: Thoroughly clean the cylinder head with cleaning solvents and brushes to remove any dirt, grease, or debris.
- Identify the Crack: Locate the crack and use a magnifying glass to assess its size and extent.
- Grind the Crack: Grind out the crack to remove any damaged or contaminated material.
- Preheat the Cylinder Head: Preheat the cylinder head in an oven to the recommended temperature (450-550 degrees F or 232-288 degrees C for aluminum, 1,300 degrees F or 704 degrees C for cast iron).
- Weld the Crack: Use a TIG welder (for aluminum) or a welding torch (for cast iron) to weld the crack, melting the surrounding metal and filling the crack with molten metal and filler rod.
- Slow Cool the Cylinder Head: Allow the cylinder head to cool slowly to relieve stress in the metal and prevent cracking.
- Smooth the Surface: Grind and smooth the surface to remove any excess material and create a flush finish.
- Pressure Test: Conduct a pressure test to ensure that the repair is effective and there are no leaks.
6. Post-Repair: Ensuring a Lasting Fix
What steps should be taken after repairing a cracked cylinder head to ensure a long-lasting fix? After repairing a cracked cylinder head, it’s crucial to take additional steps to ensure a lasting fix and prevent future problems.
6.1. Checking for Warpage: Surface Straightness is Key
How do you check for warpage after repairing a cylinder head, and why is it important? Use a straight edge and feeler gauges to check the cylinder head surface for warpage. Place the straight edge across the surface and measure the gap between the straight edge and the surface using the feeler gauges. If the warpage exceeds the manufacturer’s specifications, the cylinder head must be resurfaced to ensure a proper seal with the engine block.
6.2. Resurfacing: Achieving a Perfect Seal
Why is resurfacing important after welding a cylinder head? Resurfacing involves machining the cylinder head surface to create a flat, smooth finish. This ensures a proper seal with the engine block and prevents leaks. Resurfacing is particularly important after welding, as the heat from the welding process can cause distortion of the cylinder head surface.
6.3. Valve Job: Optimizing Performance
Why might a valve job be necessary after repairing a cracked cylinder head? A valve job involves grinding the valve seats and valves to ensure a proper seal and optimal engine performance. This may be necessary if the valve seats have been damaged or distorted during the repair process. A valve job can improve compression, increase power, and reduce emissions.
6.4. Reassembly: Precision is Paramount
What should you pay attention to during the reassembly of the cylinder head? When reassembling the cylinder head, follow the manufacturer’s specifications for torque values and bolt tightening sequences. Use new head bolts and gaskets to ensure a proper seal. Pay attention to the position of all components and ensure that they are properly installed.
6.5. Coolant System Care: Preventing Future Cracks
How can proper coolant system maintenance prevent future cylinder head cracks? Proper coolant system maintenance is essential to prevent future cylinder head cracks. Use the correct type of coolant and maintain the proper coolant level. Regularly flush and replace the coolant to remove contaminants and prevent corrosion. Also, check the cooling system for leaks and address any issues promptly.
7. Prevention: Avoiding Cracked Heads
What proactive measures can be taken to prevent cylinder head cracks? Preventing cylinder head cracks involves several proactive measures:
- Regular Maintenance: Follow the manufacturer’s recommended maintenance schedule for your vehicle.
- Coolant Checks: Regularly check and maintain the correct coolant level and concentration.
- Avoid Overheating: Monitor your engine temperature and address any overheating issues immediately.
- Proper Installation: Ensure that all engine components are installed correctly, with the proper torque values.
- Quality Parts: Use high-quality replacement parts that meet or exceed the manufacturer’s specifications.
- Driving Habits: Avoid aggressive driving habits that can put excessive stress on the engine.
- Regular Inspections: Have your engine inspected regularly by a qualified mechanic to identify and address any potential issues early.
- Address Leaks: Fix any coolant or oil leaks promptly to prevent engine damage.
- Use Additives: Consider using coolant additives that can help protect against corrosion and improve heat transfer.
- Monitor Performance: Pay attention to any changes in engine performance, such as reduced power or rough idling, and address them promptly.
By following these preventive measures, you can minimize the risk of cylinder head cracks and maintain the health of your engine.
8. Cost Considerations: Repair vs. Replacement
What factors should you consider when deciding whether to repair or replace a cracked cylinder head? When faced with a cracked cylinder head, one of the most important decisions is whether to repair or replace it. Consider these factors:
8.1. Estimating Repair Costs: What to Expect
What are the typical costs associated with repairing a cracked cylinder head using different methods? The cost of repairing a cracked cylinder head varies depending on the repair method, the extent of the damage, and the labor rates in your area. Pinning is typically the least expensive repair method, while welding can be more costly due to the specialized equipment and skills required. Expect to pay anywhere from $300 to $1,500 for pinning, and $500 to $3,000 for welding.
8.2. Assessing Replacement Costs: New vs. Used
How do the costs of new, remanufactured, and used cylinder heads compare? The cost of replacing a cylinder head depends on whether you choose a new, remanufactured, or used unit. New cylinder heads are the most expensive option, but they offer the best performance and reliability. Remanufactured cylinder heads are rebuilt to meet or exceed the manufacturer’s specifications and are typically less expensive than new units. Used cylinder heads are the least expensive option, but their condition is uncertain, and they may not last as long as new or remanufactured units.
Type of Cylinder Head | Estimated Cost | Pros | Cons |
---|---|---|---|
New | $800 – $3,000 | Best performance, highest reliability, new warranty | Most expensive |
Remanufactured | $500 – $2,000 | Rebuilt to specifications, lower cost, warranty | May not perform as well as new |
Used | $200 – $800 | Least expensive | Condition uncertain, may have limited lifespan, no warranty |
Pinning | $300 – $1,500 | Cost-effective for small cracks | Suitable for Non-critical areas |
Welding | $500 – $3,000 | Durable repair for larger cracks | Can be expensive, may cause distortion |
8.3. Labor Costs: A Significant Factor
How do labor costs influence the decision between repairing and replacing a cracked cylinder head? Labor costs can be a significant factor in the decision to repair or replace a cracked cylinder head. Repairing a cylinder head typically requires more labor hours than replacing it, as it involves cleaning, inspecting, and repairing the damaged area. Replacing a cylinder head is a more straightforward process that can be completed more quickly. Get estimates from multiple shops to compare labor costs and make an informed decision.
8.4. Long-Term Value: Weighing the Options
What are the long-term implications of repairing versus replacing a cracked cylinder head? Consider the long-term value of your vehicle and the potential for future problems when deciding whether to repair or replace a cracked cylinder head. Repairing a cylinder head may be a cost-effective solution in the short term, but it may not be as reliable as replacing it with a new or remanufactured unit. If you plan to keep your vehicle for many years, replacing the cylinder head may be the best option to ensure long-term reliability and performance.
9. Professional Help: When to Call an Expert
When should you seek professional help for a cracked cylinder head repair? While some repairs can be tackled by experienced DIY mechanics, certain situations warrant professional assistance.
9.1. Complexity of the Repair: Knowing Your Limits
When does the complexity of a cylinder head repair exceed the capabilities of a DIY mechanic? If the crack is extensive, located in a critical area, or requires specialized techniques such as welding or furnace welding, it’s best to seek professional help. These repairs require specialized equipment and skills that most DIY mechanics don’t possess. Attempting to perform complex repairs without the necessary expertise can result in further damage to the cylinder head or engine.
9.2. Lack of Experience: Avoiding Costly Mistakes
How can a lack of experience lead to costly mistakes when repairing a cracked cylinder head? If you lack experience in repairing cylinder heads, you may not be able to properly diagnose the problem, select the appropriate repair method, or perform the repair correctly. This can lead to costly mistakes, such as further damaging the cylinder head, causing leaks, or reducing engine performance. It’s better to seek professional help than to risk making costly mistakes.
9.3. Specialized Equipment: Access to the Right Tools
When is specialized equipment necessary for repairing a cracked cylinder head? Certain repairs, such as welding, furnace welding, and resurfacing, require specialized equipment that most DIY mechanics don’t have access to. Welding requires a TIG welder or welding torch, while furnace welding requires a preheating oven and slow-cooling equipment. Resurfacing requires a specialized machining tool to create a flat, smooth surface. If you don’t have access to the necessary equipment, it’s best to seek professional help.
9.4. Time Constraints: Balancing Time and Expertise
How can time constraints influence the decision to seek professional help for a cylinder head repair? Repairing a cracked cylinder head can be a time-consuming process, especially if you’re not experienced. If you have time constraints or need your vehicle back on the road quickly, it may be best to seek professional help. A professional mechanic can complete the repair more quickly and efficiently, minimizing downtime.
10. CARDIAGTECH.NET: Your Partner in Automotive Solutions
How can CARDIAGTECH.NET assist with diagnosing and repairing cracked cylinder heads? CARDIAGTECH.NET is your trusted partner for all your automotive diagnostic and repair needs. We offer a wide range of tools and equipment to help you diagnose and repair cracked cylinder heads efficiently and effectively.
10.1. Diagnostic Tools: Precision and Accuracy
What diagnostic tools does CARDIAGTECH.NET offer to help identify cracked cylinder heads? CARDIAGTECH.NET offers a comprehensive selection of diagnostic tools, including:
- Compression Testers: Measure the compression in each cylinder to identify leaks and assess engine health.
- Leak-Down Testers: Pinpoint the source of leaks by pressurizing each cylinder and measuring the rate of pressure loss.
- Pressure Testers: Check for leaks in the cooling system and cylinder head by applying air pressure to the coolant passages.
- Dye Penetrant Kits: Reveal surface cracks and imperfections with special dyes and developers.
- Borescopes: Visually inspect the inside of the cylinders and coolant passages for cracks and damage.
These diagnostic tools help you accurately identify cracked cylinder heads and determine the best course of action.
10.2. Repair Equipment: Quality and Reliability
What repair equipment does CARDIAGTECH.NET provide for fixing cracked cylinder heads? CARDIAGTECH.NET offers a wide range of repair equipment, including:
- Pinning Kits: Complete kits with drills, taps, pins, and air hammers for repairing small cracks in cast iron and aluminum cylinder heads.
- Welding Machines: TIG welders for aluminum cylinder heads and welding torches for cast iron cylinder heads.
- Grinders: High-quality grinders with various bits for removing material and smoothing surfaces.
- Measuring Tools: Straight edges, feeler gauges, and micrometers for checking warpage and ensuring precise measurements.
Our repair equipment is designed to provide quality, reliability, and ease of use, helping you complete your repairs efficiently and effectively.
10.3. Expert Advice: Guidance and Support
How does CARDIAGTECH.NET provide expert advice and support for automotive repairs? At CARDIAGTECH.NET, we’re committed to providing you with the expert advice and support you need to tackle even the most challenging automotive repairs. Our team of experienced technicians is available to answer your questions, provide guidance, and offer solutions to your problems. Whether you need help diagnosing a cracked cylinder head, selecting the right repair method, or using our tools and equipment, we’re here to help.
10.4. Contact Us Today: Get the Help You Need
Ready to tackle your cracked cylinder head repair with confidence? Contact CARDIAGTECH.NET today for expert advice, quality tools, and reliable support.
Address: 276 Reock St, City of Orange, NJ 07050, United States
WhatsApp: +1 (641) 206-8880
Website: CARDIAGTECH.NET
Don’t let a cracked cylinder head compromise your engine’s performance and reliability. Trust CARDIAGTECH.NET to provide you with the tools and expertise you need to get the job done right.
Are you facing challenges with difficult repairs, tight deadlines, or the need for specialized tools? Contact CARDIAGTECH.NET today. Let our experienced team provide you with the expert advice and support you need to streamline your work, increase accuracy, and enhance your shop’s reputation. Reach out to us now and discover how we can help you elevate your automotive repair services.
1. How much does it cost to fix a cracked cylinder head?
The cost to fix a cracked cylinder head varies based on the repair method. Pinning typically ranges from $300 to $1,500, while welding can cost between $500 and $3,000. Replacement with a new cylinder head can range from $800 to $3,000, excluding labor costs. The exact cost depends on the vehicle model, the extent of the damage, and labor rates in your area.
2. Can a cracked cylinder head be repaired instead of replaced?
Yes, a cracked cylinder head can often be repaired instead of replaced, depending on the size, location, and severity of the crack. Small cracks can be repaired using pinning, while larger cracks can be repaired using welding techniques. However, if the cylinder head is severely damaged or warped, replacement may be the only option.
3. What are the symptoms of a cracked cylinder head?
Common symptoms of a cracked cylinder head include engine overheating, white smoke from the exhaust, coolant loss, milky oil, poor engine performance, external leaks, bubbling in the radiator, a sweet smell, increased oil consumption, and a pressurized cooling system.
4. What causes cylinder heads to crack?
Cylinder heads typically crack due to thermal stress, which can be caused by overheating, rapid temperature changes, loss of coolant, detonation, improper installation, design flaws, or corrosion.
5. Is it safe to drive with a cracked cylinder head?
No, it is not safe to drive with a cracked cylinder head. A cracked cylinder head can lead to serious engine damage, including overheating, loss of compression, and oil contamination. Driving with a cracked cylinder head can also result in a breakdown and potential safety hazards.
6. How do I know if my cylinder head is warped?
You can check for warpage using a straight edge and feeler gauges. Place the straight edge across the cylinder head surface and measure the gap between the straight edge and the surface using the feeler gauges. If the warpage exceeds the manufacturer’s specifications, the cylinder head needs to be resurfaced.
7. What is the difference between TIG welding and furnace welding?
TIG welding is used for repairing aluminum cylinder heads and involves using an alternating current and an inert gas to prevent the formation of aluminum oxide. Furnace welding is used for repairing cast iron cylinder heads and involves preheating the cylinder head to a high temperature in an oven before welding.
8. Can I repair a cracked cylinder head myself?
Repairing a cracked cylinder head yourself depends on your experience, skill level, and access to specialized equipment. Simple repairs like pinning can be done by experienced DIY mechanics, while more complex repairs like welding should be left to professionals.
9. How important is it to maintain the coolant system to prevent cylinder head cracks?
Maintaining the coolant system is crucial to prevent cylinder head cracks. Regularly check and maintain the correct coolant level and concentration, flush and replace the coolant to remove contaminants, and address any leaks promptly.
10. Where can I find quality tools and equipment for repairing cylinder heads?
You can find quality tools and equipment for repairing cylinder heads at CARDIAGTECH.NET. We offer a wide range of diagnostic tools, repair equipment, and expert advice to help you tackle even the most challenging automotive repairs.